Transporte automático y conveyor
Las soluciones logísticas de transporte automático incrementan notablemente la productividad, eliminando la mano de obra y manteniendo la cadencia y flujos necesarios en los procesos de producción y preparación de pedidos
En ULMA Handling Systems ofrecemos un amplio surtido de sistemas inteligentes de transporte tales como VTD, STV, AGV, transportadores motorizados, transportadores de gravedad, transportadores de palets, mesas de giro, transfers, elevadores, curvas motorizadas...
Los sistemas inteligentes de transporte se emplean fundamentalmente para cubrir necesidades de transporte de cargas entre varios puntos. Normalmente su uso se combina con el de un sistema de transportadores.
Si necesitas más información sobre nuestros productos, contáctanos.
A continuación te explicamos los siguientes puntos:
- Qué es el Conveying, ¿cómo se transportan los materiales?
- Qué es el transporte de cargas ligeras
- Qué son los transportadoes de palets
- Otos sistemas de transporte continuo
- Sistemas de transporte discontinuo
- Qué son los AGV o vehículos con guiado automático
- Cuál es la evolución de los sistemas de conveyor
- Beneficios de los sistemas de transporte automático
Conveying, ¿Cómo se transportan los materiales?
Todos los materiales necesitan ser transportados entre los distintos procesos de una empresa, desde el camión al almacén, desde el almacén a un proceso, y también entre diferentes procesos.
Este transporte puede ser realizado de manera manual o automática con tecnologías muy diversas en función de la naturaleza del material. Es muy diferente transportar líquidos y gases, que solidos a granel o bultos empaquetados y/o agrupados.
Nosotros vamos a centrarnos aquí de las tecnologías utilizadas para el transporte automático de bultos empaquetados, cajas y palets con un grupo de cajas o paquetes.
La primera clasificación que vamos a realizar es en función del tamaño y peso del bulto y la segunda si el transporte se realiza de manera continua o discontinua.
Así, podemos analizar los sistemas para el transporte de cargas ligeras (hasta aproximadamente 100Kg), o de paletas (pueden ser paletas, cestones o paquetes) de 500 Kg, 1000 kg o más.
Transporte de cargas ligeras
Dentro de las cargas ligeras los sistemas más frecuentemente utilizados son los transportadores o cintas. Estas suelen ser de rodillos o de bandas, también de bandas modulares y de cadenas plásticas.
Los transportadores de rodillos desplazan la carga mediante el giro de estos y el rozamiento generado entre el rodillo y el producto que hace que este se mueva. Pueden ser en recta o en curva, normalmente en un plano horizontal y con la finalidad de solo transportar o también procesar los bultos o acumularlos.
Existen diferentes tecnologías para ello, como la utilización de motores externos y trasmisión a cada rodillo o la utilización de rodillos motorizados y trasmisión entre rodillos.
Estos sistemas se complementan con transferencias, empujadores o desviadores para pasar de una línea a otra en el mismo plano, y elevadores para pasar de un plano a otro en vertical.
Los transportadores o cintas de bandas están compuestas por una banda cerrada, normalmente de PVC, que se desplaza entre dos rodillos, con una cara superior de tracción y otra inferior de reenvío, y que desplaza el bulto situado en la cara de tracción. Uno de los dos rodillos, o un tercer rodillo se encuentra motorizado y es el que genera la tracción a la banda.
Para el desvío de los bultos a otra línea se debe realizar por inyección a gran velocidad o empujadores. En vertical pueden utilizarse elevadores, aunque también es habitual utilizar el mismo transportador de banda inclinada, de subida o bajada, y hacerlo de manera continua.
Similar a la banda de PVC es la banda modular, cuyo principio de funcionamiento es similar, pero su construcción es a base de piezas plásticas enlazadas como los eslabones de cadenas.
Existen también tramos rectos y curvos, y son muy adecuados en las instalaciones donde se precisa de limpieza, aunque el grado de fricción es inferior al PVC por lo que las bandas inclinadas no permiten ángulos tan pronunciados. Para el cambio de nivel existe el Spiralveyor que es una banda en espiral para la reducción del área utilizada.
Por último, hacer mención a las cadenas plásticas, o de charnelas, cuya función es idéntica a la anterior, pero que es utilizado en cadenas productivas donde el bulto a transportar es pequeño y mucho más ligero.
En cuanto a las productividades obtenidas con los transportadores de rodillos y bandas pueden ir desde los 1.000-2.000 cajas/hora hasta 5.000-6.000 cajas/hora, si bien hay elementos limitantes que hacen que los flujos sean menores. Además de la velocidad, 30 m/min a 90 m/min e incluso mayores, hay que tener en cuenta factores como la estabilidad del bulto, su inercia en caso de líquidos, coeficiente de fricción del material, forma de la base, plana o estriada, y calidad del bulto.
Transportadores de palets
Para los palets, los sistemas continuos son muy parecidos a los de cargas ligeras, pero con un diseño y dimensionamiento acorde a sus dimensiones y pesos.
La diferencia es que en los rodillos se utilizan mesas de giro en lugar de curvas, por su complejidad de ejecución, y los transfers son de cadenas en lugar de correas.
Las mesas de giro son elementos que neumáticamente o eléctricamente giran una mesa normalmente 90º y tienen un transportador sobre esta mesa para su carga y descarga.
Los transportadores de banda son sustituidos por transportadores de cadena, todos en un plano horizontal, no hay elevación continua, y la paleta se apoya en 2 o 3 cadenas en función del peso y de la flexión admisible de la propia paleta. Si esta es de calidad pobre o se prefiere no correr riesgos, se pone un travesaño entre las cadenas convirtiéndose en un transportador de tablillas o “slat conveyor”.
Los transfers son de cadenas y existen mesas de giro de cadenas.
No se utilizan de banda de PVC, ni banda modular.
Las productividades alcanzadas son en torno a las 200 Paletas/hora, si bien es requerido arrancadores o variadores de frecuencia y la estabilidad de la propia carga debe permitirlo.
Otros sistemas de transporte continuo
Otros transportadores continuos son utilizados en nichos muy específicos para problemáticas determinadas. Por ejemplo, los transportadores aéreos, mediante cadena continua, o el denominado power&free, con un doble circuito, uno para la cadena con movimiento continuo y otro para el guiado de los carros porteadores que pueden ser enganchados o liberados de la cadena en ciertas posiciones. Así los carros pueden circular y cambiar de circuito, pueden pararse para alguna operación, pasar a un circuito de velocidad inferior por ejemplo para montaje, carga o descarga, o también acumular entre procesos.
Estos transportadores aéreos son utilizados en el sector textil para prendas colgadas, para el e-commerce con bolsas que pueden adecuarse fácilmente a diferentes morfologías de productos, en la industria del automóvil, etc…
Una variante al transportador aéreo es la cadena enterrada, con una filosofía de trabajo similar pero que las cargas van apoyadas en el suelo. Este es más adecuado para paletas y otras cargas pesadas como por ejemplo bobinas de papel, si bien está siendo desplazado por otros sistemas discontinuos que evitan la necesidad de obra civil para la adecuación del edificio, y son mucho más flexibles si se requiere un cambio de circuito.
Sistemas de transporte discontinuos
En cuanto a los sistemas discontinuos, aunque teóricamente todos son vehículos guiados, en la práctica se distinguen entre los que precisan un sistema de guiado fijo y los que no.
Esta tecnología se basa en vehículos que transportan la carga encima y que tiene un punto de origen y uno de destino (from-to) y muchas veces se asemeja al transporte de personas mediante autobuses o taxis.
Los que necesitan de un sistema de guiado fijo, están los Transfer-carts con railes en el suelo, sobre el suelo o enterrados, y que trabajan en línea, con el vehículo circulando en dos sentidos, o en bucle cerrado, que permite utilizar más vehículos pero que todos recorren el trayecto en el mismo sentido. Sería similar a un circuito de autobuses que recorren un trayecto y tienen varias paradas de carga/descarga.
Las electrovías, son unos carros que se mueven colgados de un rail situado en el techo, fijo a él o a unas columnas soportes desde el suelo. Cada carro es autónomo y lleva una o más cargas. En el caso de las electrovías pueden existir cambios de rail, de manera que el vehículo puede seleccionar un camino u otro, sin embargo, estos desvíos hay que ponerlos solo si es claro su utilización porque es un coste añadido y perjudica el flujo en ese punto.
Todos estos sistemas trabajan habitualmente en entornos cerrados con acceso prohibido de operarios por el peligro que supone. Solo las electrovías pueden trabajar en entornos abiertos, pero solo si la velocidad de los vehículos es muy baja y la normativa lo permite.
Los sistemas de carros con guiado fijo suelen trabajar con paletas o similar, y sus productividades dependen del sistema, pero pueden llegar de 100-200 a 400-500 paletas/hora transportadas en los sistemas más eficientes.
Vehículos con guiado automático
Por último, están los sistemas de vehículos con guiado automático, son los AGVs o AMRs, que trabajan con un sistema de guiado, pero sin guías fijas. Son sistemas más flexibles pues pueden cambiarse con mayor rapidez y menor costo, más o menos inteligentes y rápidos, y aunque inicialmente fueron utilizados para el transporte de paletas, recientemente son también aplicados con cajas y piezas.
Los AGVs, Automated Guided Vehicles, tienen un sistema de navegación que le permite desplazarse por unos circuitos predeterminados. Los sistemas de navegación pueden ser magnetoguiados o filoguiados, por tags magnéticos, laserguiados, por lectura de etiquetas datamatrix en el suelo, y últimamente por Slam Lidar based.
Los circuitos definidos pueden ser muy variados y tener uniones y desvíos que permiten crear zonas de paso, zonas de espera, atajos, y otros.
El AGV en caso de detectar un obstáculo que le imposibilite seguir se para y espera a que el obstáculo sea retirado para proseguir.
Normalmente trabajan en entornos abiertos, aunque existen instalaciones en entornos cerrados donde los vehículos no tienen un sistema de detección de personas suficientemente fiables para el trabajo a las velocidades a las que trabaja.
Los AMRs, Autonomus Mobile Robots, normalmente trabajan con sistema Slam Lidar based. También pueden ser basados en datamatrix.
Lo que les hace diferentes a los AGVs es que el robot no trabaja con circuitos predefinidos, sino que una vez conocido el origen y el destino y conocido el entorno, calculan la ruta más eficiente para completar la misión. Durante el trayecto, están en constante vigilancia por si el entorno ha cambiado y en ese caso, recalculan automáticamente a una nueva trayectoria evitando el obstáculo.
Los flujos dependen en menor medida de la velocidad del vehículo, y fundamentalmente de las distancias a recorrer, y estas pueden ser desde pocos metros, a cruzar una fábrica de punta a punta.
Además, la cantidad de vehículos influye cuando en zonas un vehículo tiene que esperar al otro.
Así, cada vehículo podría llegar a hacer desde 10-15 paletas/hora hasta 25-30 paletas/hora.
Evolución de los sistemas de conveyor
En definitiva, los sistemas descritos permiten automatizar la movimentación de las mercancías dentro de la fábrica y cumplir de manera más eficiente con la misión del mismo:
Mover las mercancías dentro de la empresa de la manera más eficiente uniendo los orígenes y los destinos, y cumpliendo con la producción requerida.
Aunque los sistemas continuos poseen una capacidad superior en la producción de movimientación, recientemente los sistemas basados en vehículos están experimentando un auge debido a las ventajas que poseen de flexibilidad, reducción drástica de las puestas a punto y consiguiente inmediatez, reutilización para funciones o localizaciones diferentes, y estandarización consiguiendo plazos de entrega más cortos.
Beneficios de los sistemas de transporte automático:
En definitiva, las ventajas asociadas con la automatización del transporte son:
- Reducción de costes de transporte interno en la fábrica y por tanto ahorros de coste de producción o preparación.
- Reducción de la mano de obra en la manipulación y aumento de la productividad de los operarios.
- Aumento de la seguridad, evitando numerosos accidentes derivados de la manipulación manual.
- Generar un flujo más coordinado y eficiente entre procesos, derivado de una limitación de los propios sistemas.
- Asegurar una asociación entre el movimiento físico de los materiales y el movimiento lógico en los sistemas de gestión.
- Garantizar la trazabilidad en productos sensibles como alimentos o medicamentos.

Descrambling
El descrambling garantiza una perfecta individualización de los productos previamente separados en capas
Más información
Transportadores de palets
Permiten un transporte flexible y eficaz en distancias largas
Más información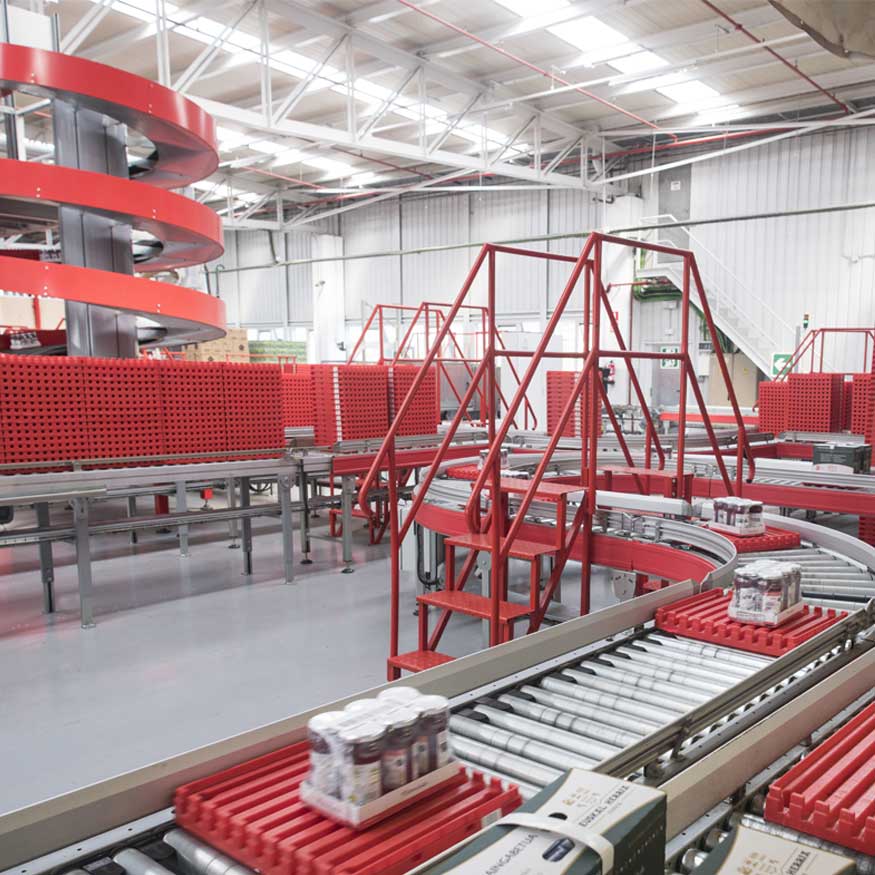
Transportadores carga ligera
Diseñados para el transporte de productos almacenados en cajas de cartón y/o plástico, contenedores y bandejas de hasta 50kg
Más información
Automated Guided Vehicle (AGV)
Sistemas inteligentes de transporte completamente automáticos y flexibles que no requieren de intervención humana
Más información
Sorting Transfer Vehicle (STV)
El Sorting Transfer Vehicle (STV) es el sistema inteligente de transporte que se caracteriza por su fiabilidad y rapidez, con capacidad de movimiento de 800 transferencias/hora
Más información
Shuttle Carts
Sistemas inteligentes de transporte de transferencia de control autónomo destinados a operaciones de transporte entre estaciones motorizadas
Más información
BESA
BESA (Bernardo Ecenarro) abre sus puertas a la automatización de la mano de ULMA Handling Systems
Más información
EROSKI Madrid M50
Sistema pionero de preparación de pedidos totalmente automático
Más información
ENTREPINARES
La logística apuesta por la calidad de producto
Más información
BONDUELLE
Sistema logístico a temperatura controlada
Más información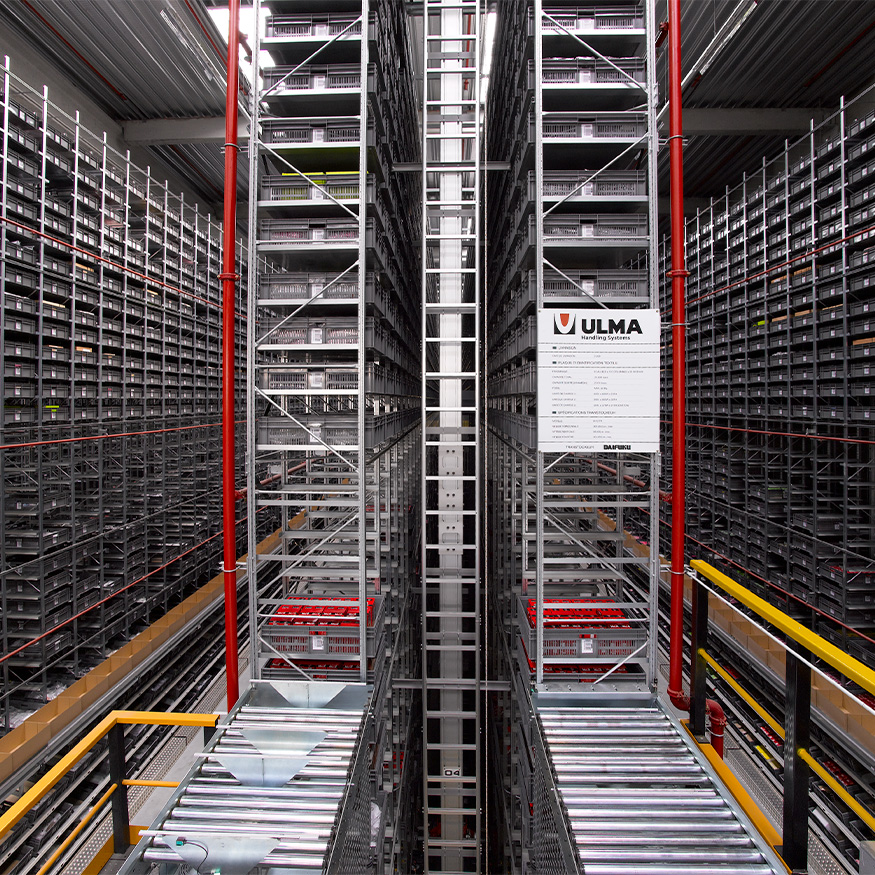
SYSTEME U
Optimización logística para la cadena de distribución francesa SYSTÉME U
Más información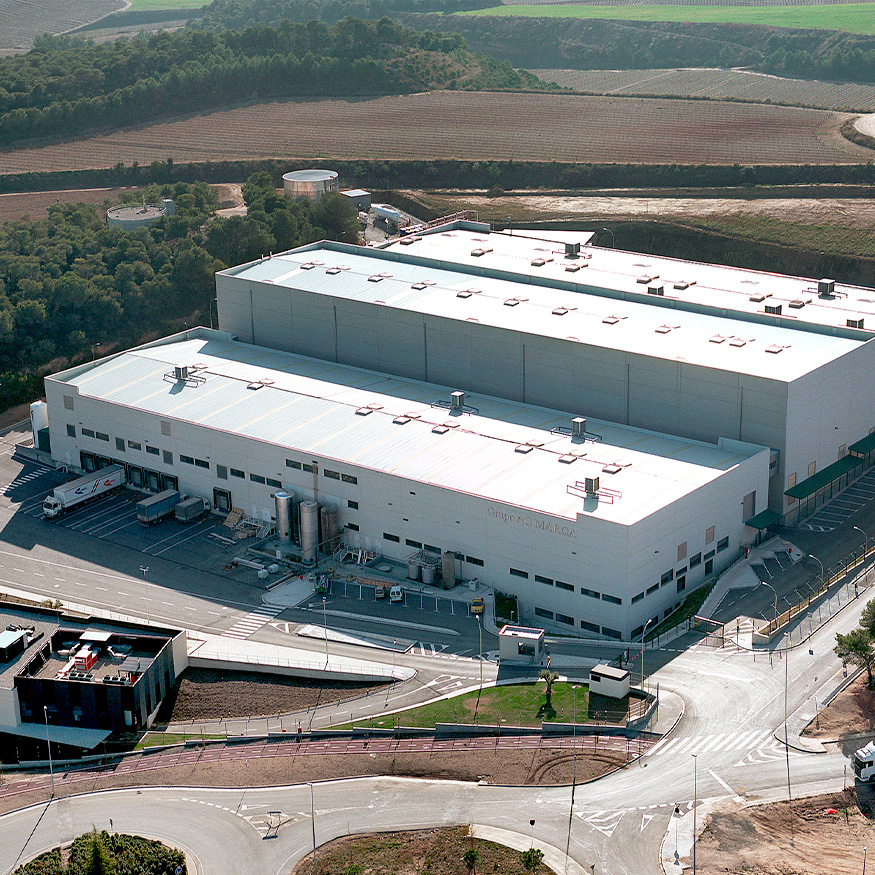
AC MARCA
Automatizar para ganar competitividad
Más informaciónHabla con nosotros
¿Quieres mejorar tu productividad y ser más eficiente en tu logística?
Solicita información