Soluções de transporte automático
As soluções logísticas de transporte automático incrementam notavelmente a produtividade, eliminando a mão de obra e mantendo a cadência e fluxos necessários nos processos de produção e separação de pedidos
Na ULMA Handling Systems oferecemos um amplo surtido de logística do transporte automático tais como VTD, STV, AGV, transportadores motorizados, transportadores de gravidade, mesas de giro, transfers, elevadores, curvas motorizadas...
O logística do transporte automático se utilizam fundamentalmente para cobrir necessidades de transporte de cargas entre vários pontos. Normalmente seu uso se combina com o de um sistema de transportadores.
Se você quiser obter mais informações do sistemas inteligentes de transporte automático, entre em contato conosco.
Transporte, como os materiais são transportados?
Todos os materiais precisam ser transportados entre os diferentes processos de uma empresa, do caminhão ao depósito, do depósito a um processo e também entre diferentes processos.
Esse transporte pode ser realizado manual ou automaticamente com tecnologias muito diferentes, dependendo da natureza do material. É muito diferente transportar líquidos e gases, sólidos a granel ou pacotes embalados e/ou agrupados.
Vamos nos concentrar aqui nas tecnologias usadas para o transporte automático de embalagens, caixas e paletes com um grupo de caixas ou embalagens.
A primeira classificação que faremos se baseia no tamanho e no peso da embalagem e a segunda no fato de o transporte ser realizado de forma contínua ou descontínua.
Assim, podemos analisar os sistemas para o transporte de cargas leves (até aproximadamente 100 kg), ou paletes (podem ser paletes, cestas ou pacotes) de 500 kg, 1000 kg ou mais.
Transporte de cargas leves
Os sistemas usados com mais frequência para cargas leves são transportadores ou correias. Em geral, são transportadores de roletes ou correias, bem como correias modulares e correntes plásticas.
Os transportadores de roletes movimentam a carga por meio da rotação dos roletes e do atrito gerado entre o rolete e o produto que o faz se mover. Eles podem ser retos ou curvos, normalmente em um plano horizontal e com a finalidade de apenas transportar ou também processar as embalagens ou acumulá-las.
Existem diferentes tecnologias para isso, como o uso de motores externos e a transmissão para cada rolo ou o uso de rolos motorizados e a transmissão entre os rolos.
Esses sistemas são complementados com transferências, empurradores ou desviadores para mover de uma linha para outra no mesmo plano, e elevadores para mover de um plano para outro verticalmente.
Os transportadores de correia ou esteiras são compostos por uma correia fechada, normalmente de PVC, que se move entre dois rolos, com uma face de tração superior e uma face de retorno inferior, e que move o pacote localizado na face de tração. Um dos dois rolos, ou um terceiro rolo, é motorizado e gera a tração para a correia.
Para desviar os pacotes para outra linha, isso deve ser feito por injeção de alta velocidade ou empurradores. Os elevadores podem ser usados verticalmente, embora também seja comum usar o mesmo transportador de correia inclinado, para cima ou para baixo, e fazê-lo continuamente.
Semelhante à esteira de PVC é a esteira modular, cujo princípio de funcionamento é semelhante, mas sua construção é baseada em peças plásticas ligadas entre si como elos de corrente.
Há também seções retas e curvas, e elas são muito adequadas para instalações onde a limpeza é necessária, embora o grau de atrito seja menor do que o do PVC, de modo que as esteiras inclinadas não permitem ângulos tão acentuados. Para a mudança de nível, há o Spiralveyor, que é uma esteira em espiral para reduzir a área utilizada.
Por fim, cabe mencionar as correntes de plástico ou correntes articuladas, cuja função é idêntica à anterior, mas que são usadas em linhas de produção em que a embalagem a ser transportada é pequena e muito mais leve.
Quanto à produtividade obtida com os transportadores de roletes e de correia, ela pode variar de 1.000 a 2.000 caixas/hora a 5.000 a 6.000 caixas/hora, embora existam elementos limitadores que fazem com que os fluxos sejam menores. Além da velocidade, de 30 m/min a 90 m/min e até mais, devem ser levados em conta fatores como a estabilidade da embalagem, sua inércia no caso de líquidos, o coeficiente de atrito do material, a forma da base, plana ou com nervuras, e a qualidade da embalagem.
Transportadores de paletes
Para transportar paletes, os sistemas contínuos são muito semelhantes aos de cargas leves, mas com um projeto e dimensionamento de acordo com suas dimensões e pesos.
A diferença é que os roletes usam mesas giratórias em vez de curvas, devido à sua complexidade de execução, e as transferências são feitas por correntes em vez de correias.
As mesas giratórias são elementos que giram pneumática ou eletricamente uma mesa, normalmente em 90º, e possuem um transportador sobre essa mesa para carga e descarga.
Os transportadores de correia são substituídos por transportadores de corrente, todos em um plano horizontal, sem elevação contínua, e o palete é sustentado por 2 ou 3 correntes, dependendo do peso e da reflexão admissível do próprio palete. Se o palete for de baixa qualidade ou se for preferível não correr riscos, uma barra transversal é colocada entre as correntes, tornando-o um transportador de ripas.
As transferências são feitas de correntes e há mesas giratórias de correntes.
Não são usadas correias de PVC nem correias modulares.
As taxas de produção alcançadas são de cerca de 200 paletes/hora, embora sejam necessários acionadores de partida ou variadores de frequência, e a estabilidade da própria carga deve permitir isso.
Outros sistemas de transportadores contínuos
Outros transportadores contínuos são usados em nichos muito específicos para problemas específicos. Por exemplo, transportadores aéreos que usam uma corrente contínua, ou o chamado power&free, com um circuito duplo, um para a corrente com movimento contínuo e outro para guiar os carrinhos que podem ser engatados ou liberados da corrente a partir de determinadas posições. Dessa forma, os carrinhos podem circular e mudar de circuito, podem parar para uma operação, passar para um circuito de menor velocidade para montagem, carga ou descarga, ou acumular-se entre os processos.
Esses transportadores aéreos são usados no setor têxtil para pendurar roupas, para comércio eletrônico com sacolas que podem ser facilmente adaptadas a diferentes morfologias de produtos, no setor automotivo, etc.
Uma variante do transportador aéreo é o transportador de corrente subterrâneo, com uma filosofia de trabalho semelhante, mas com as cargas apoiadas no solo. Ele é mais adequado para paletes e outras cargas pesadas, como bobinas de papel, embora esteja sendo substituído por outros sistemas descontínuos que evitam a necessidade de obras civis para adaptar o edifício e são muito mais flexíveis se for necessária uma mudança de circuito.
Sistemas de transporte descontínuos
Em termos de sistemas descontínuos, embora teoricamente todos sejam veículos guiados, na prática é feita uma distinção entre os que exigem um sistema de orientação fixo e os que não exigem.
Essa tecnologia é baseada em veículos que carregam a carga e têm um ponto de origem e um ponto de destino (de-para) e geralmente é semelhante ao transporte de pessoas por ônibus ou táxi.
Os que requerem um sistema de orientação fixo são os carrinhos de transferência com trilhos no solo, acima do solo ou enterrados, e que funcionam em linha, com o veículo circulando em duas direções, ou em um circuito fechado, que permite o uso de mais veículos, mas todos percorrem a rota e têm várias paradas de carga/descarga.
As eletrovias são carrinhos que se movimentam pendurados em um trilho localizado no teto, fixado a ele ou a colunas apoiadas no chão. Cada carrinho é autônomo e transporta uma ou mais cargas. No caso das eletrovias, pode haver mudanças de trilho, de modo que o veículo possa escolher um caminho ou outro; no entanto, esses desvios só devem ser instalados se estiver claro que serão usados, pois representam um custo adicional e prejudicam o fluxo naquele ponto.
Todos esses sistemas geralmente funcionam em ambientes fechados, onde o acesso dos operadores é proibido devido ao perigo envolvido. Somente os sistemas de monotrilho eletrificado podem funcionar em ambientes abertos, mas somente se a velocidade dos veículos for muito baixa e as normas permitirem.
Os sistemas de trólebus com guia fixa geralmente trabalham com paletes ou similares, e sua produtividade depende do sistema, mas pode chegar a 100-200 a 400-500 paletes/hora transportados nos sistemas mais eficientes.
Veículo guiado automaticamente
Por fim, há os sistemas de veículos ou carros guiados automaticamente, os AGVs ou AMRs, que funcionam com um sistema de orientação, mas sem guias fixas. São sistemas mais flexíveis, pois podem ser alterados mais rapidamente e com menor custo, mais ou menos inteligentes e rápidos, e, embora tenham sido usados inicialmente para o transporte de paletes, recentemente também foram aplicados a caixas e peças.
Os AGVs, Automated Guided Vehicles (veículos guiados automaticamente), têm um sistema de navegação que permite que eles se movimentem ao longo de circuitos predeterminados. Os sistemas de navegação podem ser magnetoguiados ou filoguiados, por etiquetas magnéticas, guiados por laser, por leitura de etiquetas de matriz de dados no solo e, ultimamente, por Slam Lidar.
Os circuitos definidos podem ser muito variados e ter cruzamentos e desvios que permitem a criação de zonas de passagem, zonas de espera, atalhos e outros.
Se o AGV detectar um obstáculo que impossibilite a continuação, ele para e espera que o obstáculo seja removido antes de continuar.
Normalmente, eles trabalham em ambientes abertos, embora existam instalações em ambientes fechados em que os veículos não têm um sistema de detecção de pessoas suficientemente confiável para trabalhar nas velocidades em que trabalham.
Os AMRs, robôs móveis autônomos, normalmente trabalham com sistemas baseados em Slam Lidar. Eles também podem se basear em matrizes de dados.
O que os torna diferentes dos AGVs é que o robô não trabalha com circuitos predefinidos, mas, uma vez que a origem e o destino são conhecidos e o ambiente é conhecido, eles calculam a rota mais eficiente para concluir a missão. Durante a jornada, eles ficam constantemente atentos a mudanças no ambiente e, nesse caso, recalculam automaticamente uma nova trajetória para evitar o obstáculo.
Os fluxos dependem, em menor escala, da velocidade do veículo e, principalmente, das distâncias a serem percorridas, que podem variar de alguns metros até a travessia de uma fábrica de ponta a ponta.
Além disso, o número de veículos influencia quando, nas zonas, um veículo precisa esperar pelo outro.
Assim, cada veículo poderia fazer de 10 a 15 paletes/hora a 25 a 30 paletes/hora.
Evolução dos sistemas de transportadores
Em resumo, os sistemas descritos acima possibilitam automatizar a movimentação de mercadorias dentro da fábrica e cumprir sua missão com mais eficiência:
Movimentar mercadorias dentro da empresa da maneira mais eficiente, ligando origens e destinos e cumprindo a produção necessária.
Embora os sistemas contínuos tenham uma capacidade superior de movimentar a produção, recentemente os sistemas baseados em veículos estão experimentando um boom devido às suas vantagens de flexibilidade, redução drástica na configuração e consequente imediatismo, reutilização para diferentes funções ou locais e padronização, resultando em prazos de entrega mais curtos.
Benefícios dos sistemas de transporte automatizado:
Em última análise, os benefícios associados ao transporte automatizado são:
- Redução dos custos de transporte interno na fábrica e, portanto, economia nos custos de produção ou preparação.
- Redução da mão de obra no manuseio e aumento da produtividade dos operadores.
- Aumento da segurança, evitando inúmeros acidentes causados pelo manuseio manual.
- Gerar um fluxo mais coordenado e eficiente entre os processos, derivado de uma limitação dos próprios sistemas.
- Garantir uma associação entre a movimentação física dos materiais e a movimentação lógica nos sistemas de gerenciamento.
- Garantir a rastreabilidade em produtos sensíveis, como alimentos ou medicamentos.

Descrambling
O descrambling garante uma perfeita individualização dos produtos previamente separados em níveis
Mais informações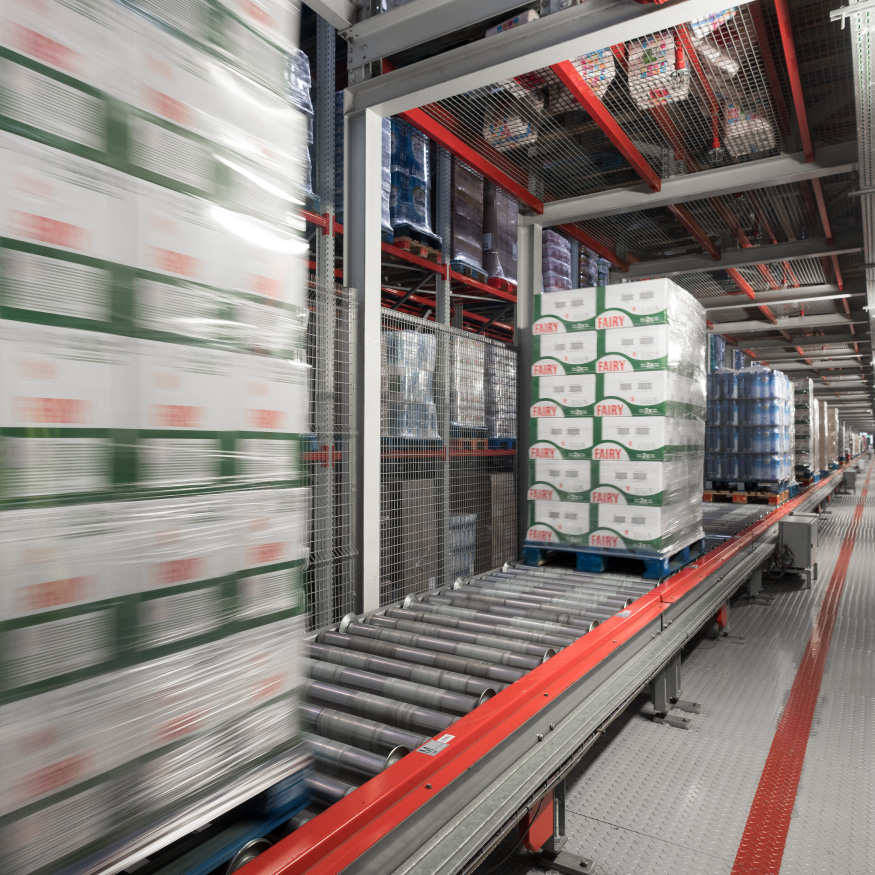
Transportadores de paletes
Permitem um transporte flexível e eficaz em distâncias longas
Mais informações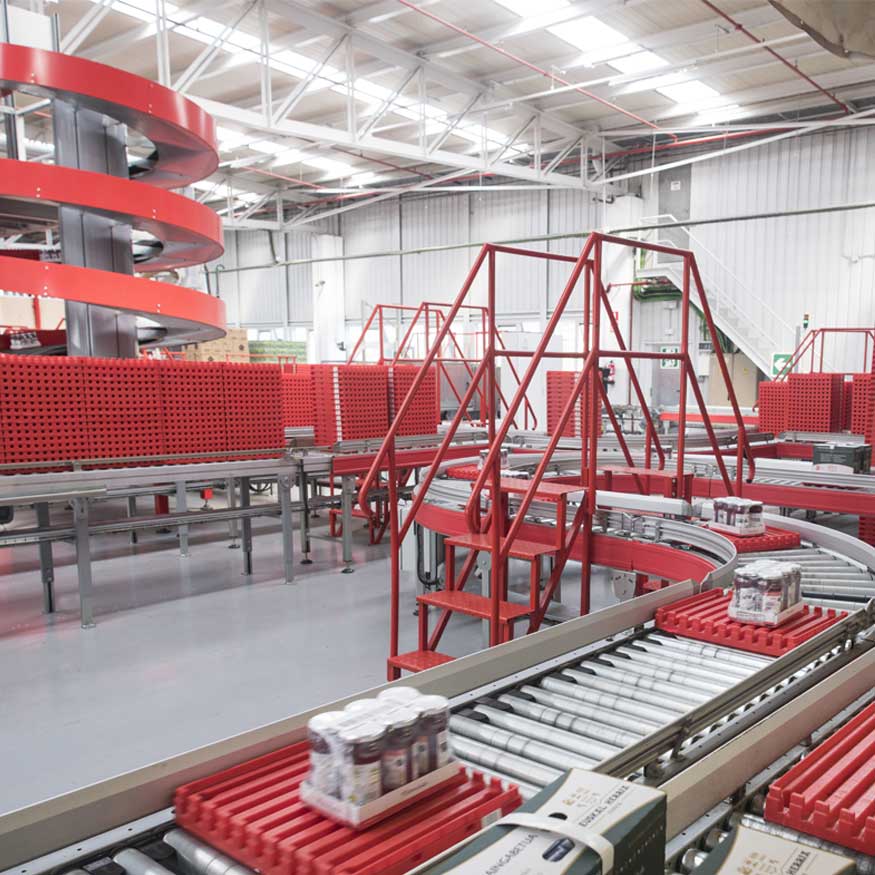
Transportadores carga leve
Projetados para o transporte de produtos armazenados em caixas de papelão e/ou plástico, contêineres e bandejas de até 50 kg
Mais informações
Automated Guided Vehicle (AGV)
Sistemas inteligentes de transporte completamente automáticos e flexíveis que não requerem intervenção humana
Mais informações
Sorting Transfer Vehicle (STV)
O Sorting Transfer Vehicle (STV) é o sistema inteligente de transporte que se caracteriza por sua fiabilidade e rapidez, com capacidade de movimento de 800 transferências/hora
Mais informações
Shuttle Carts
Sistemas inteligentes de transporte de transferência de controle autônomo destinados a operações de transporte entre estações motorizadas
Mais informações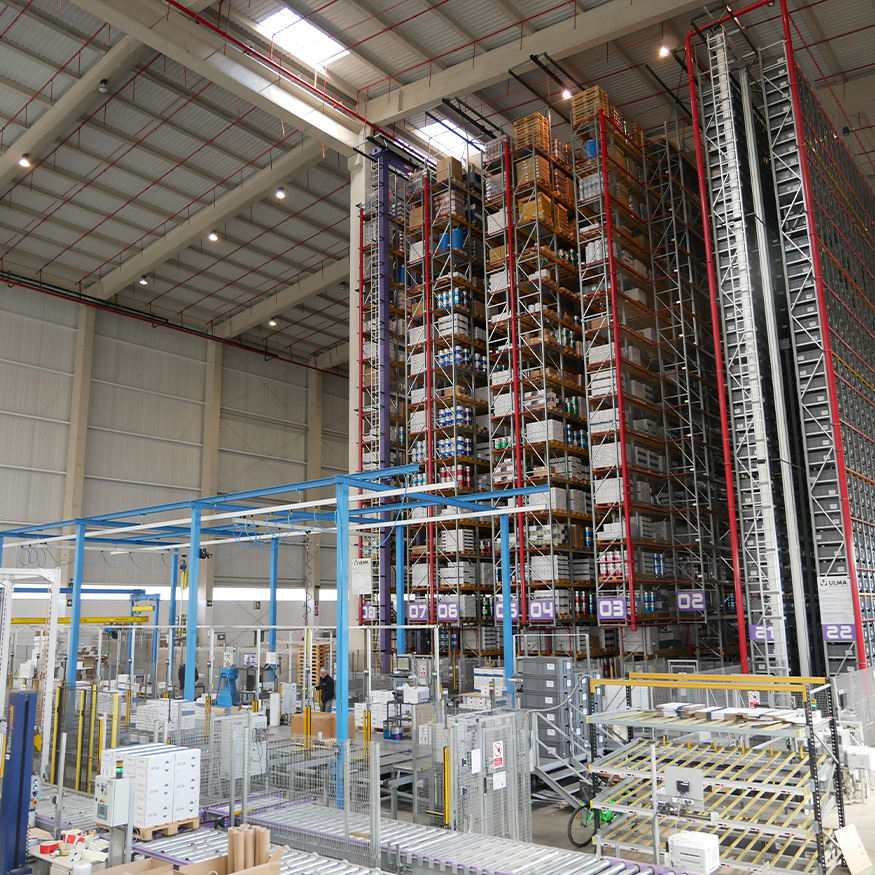
BESA
A BESA (Bernardo Ecenarro) abre suas portas para a automatização através da ULMA Handling Systems
Mais informações
EROSKI Madrid M50
Sistema pioneiro de preparação de pedidos totalmente automático
Mais informações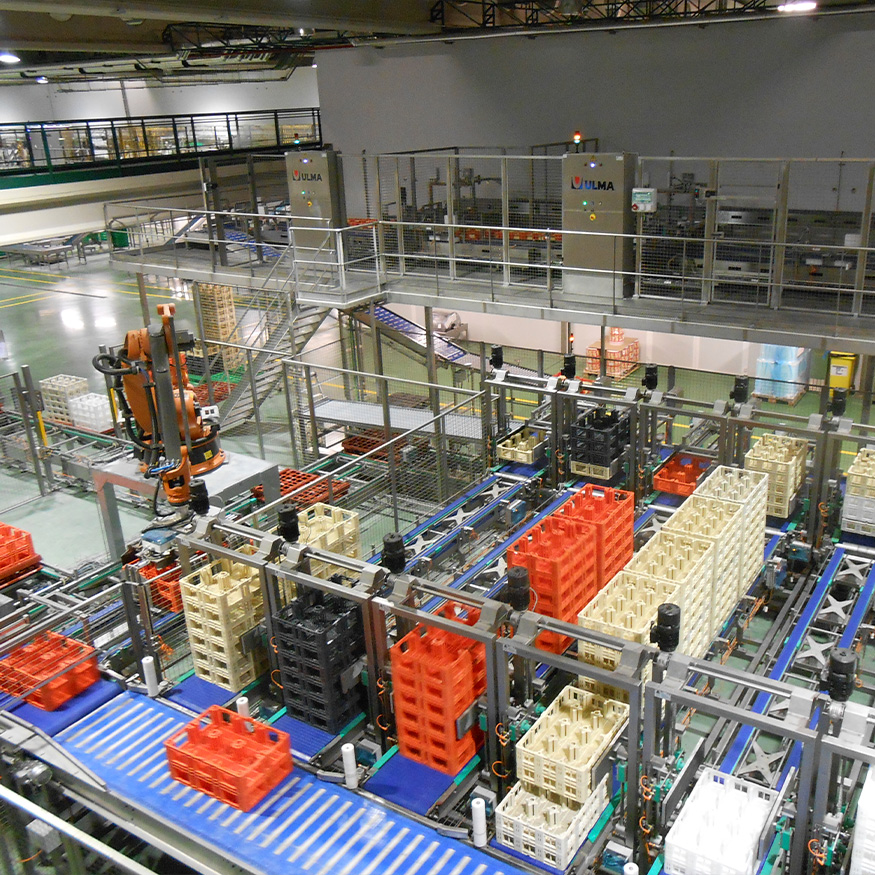
ENTREPINARES
A logística aposta pela qualidade do produto
Mais informações
BONDUELLE
Sistema logístico com temperatura controlada
Mais informações
SYSTEME U
Otimização logística para a cadeia de distribuição francesa SYSTÉME U
Mais informações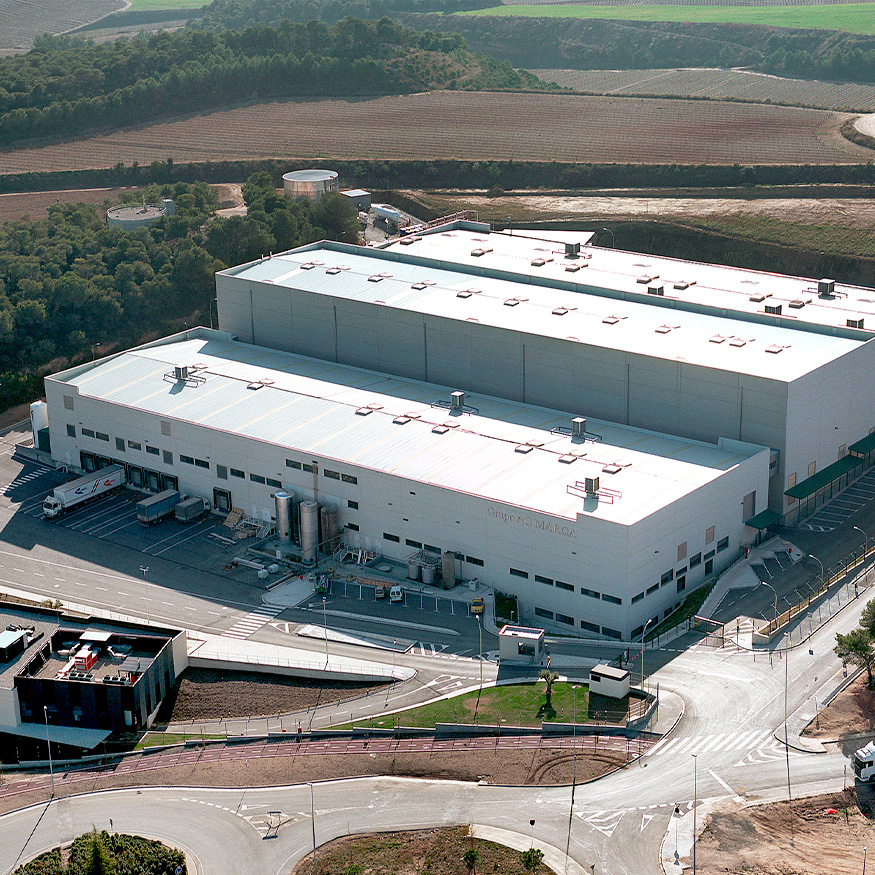
AC MARCA
Automatizar para ganhar competitividade
Mais informaçõesFale com a gente
Quer melhorar sua produtividade e ser mais eficiente na sua logística?
Solicite informação